Specialist positioning subsystems provide core building blocks in 3D surface measurement and inspection solutions for the semiconductor industry
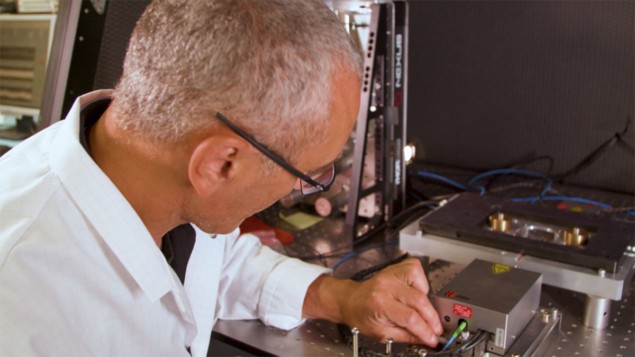
Sister companies Prior Scientific and Queensgate offer a diversified portfolio of enabling technologies to underpin the high-speed, high-precision positioning requirements of 3D optical metrology systems used in semiconductor manufacturing and applied R&D. Physics World talked to Queensgate product manager Craig Goodman about emerging technology and commercial opportunities within the semiconductor supply chain.
Why is non-contact surface metrology critical in semiconductor manufacturing?
As the semiconductor industry transitions from 8 inch to 12 inch (300 mm) wafers and smaller features on those wafers (down to 5 nm or thereabouts), optical inspection of those nanoscale features – reliable, repeatable and with high speed and high precision – becomes ever-more important. Put simply, 3D optical metrology is a must-have, with the requirement for automated surface inspection systems capable of evaluating hundreds of thousands of microelectronic devices on a single 300 mm wafer. This is where our positioning stages come into their own: a real “sweet spot” for the piezoelectric nanopositioning subsystems and capacitive sensors that we manufacture.
What does your addressable customer base look like in the semiconductor industry?
At Prior Scientific and Queensgate, we are targeting instrumentation OEM manufacturers who will integrate our range of enabling technologies into the next generation of non-contact optical metrology systems for 3D surface profiling and inspection. Upstream in the innovation chain, we also sell a range of positioning systems to semiconductor scientists and engineers working in applied R&D settings.
How do your positioning products benefit semiconductor manufacturers?
Once incorporated into OEM optical inspection systems, our products are used to support materials and device-level prototype development within semiconductor R&D labs. In the volume manufacturing environment, those same surface metrology systems are critical for quality assurance and quality control, weeding out device defects and failures at the wafer level – i.e. before those devices are incorporated into packaged electronic components. The payback is clear: by identifying defects early in the testing cycle, semiconductor manufacturers avoid those defective devices being built into a complete package and discovered further down the production line during electrical testing.
Strategically, why are Prior Scientific and Queensgate putting so much emphasis on the semiconductor market right now?
There are converging growth opportunities opening up for technology suppliers to the semiconductor industry. At a headline level, there’s the issue of semiconductor security linked to regional chip shortages during the COVID pandemic. By way of response, US, European and UK policy-makers are moving proactively to scale up domestic capacity in semiconductor production. There’s a parallel technology driver as volume manufacturing transitions to 300 mm semiconductor wafers, with instrumentation OEMs having to re-engineer their optical metrology systems accordingly. What the semiconductor industry wants, as standard, is high-throughput, scalable and automated optical inspection systems to drive workflow efficiencies and product quality.
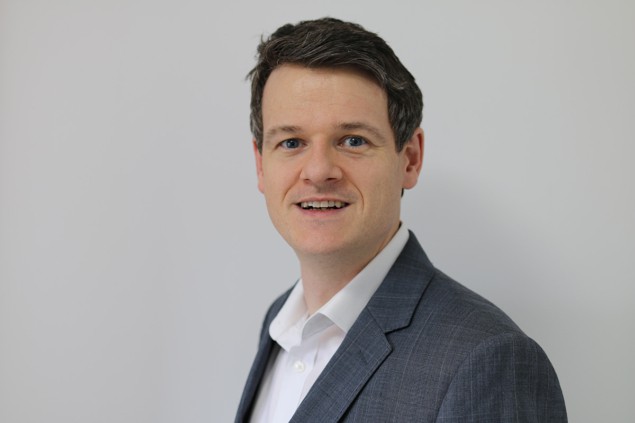
Presumably the quantum technology industry is also a driver of growth for semiconductor companies?
Correct. Advances in quantum sensing, quantum networking and quantum computing promise to yield game-changing technologies and applications, with significant areas of materials R&D and device development reliant on traditional semiconductor fabrication processes. Things are moving fast, with companies across the emerging quantum supply chain hoping to progress from the R&D lab towards sustainable commercial applications sooner rather than later.
How do Prior Scientific and Queensgate stay ahead of the curve when it comes to product innovation?
We work closely with the research community to fast-track our in-house technology innovation. A notable case study in this regard is our ongoing R&D collaboration with the National Physical Laboratory (NPL), the UK’s National Measurement Institute. With funding from Analysis for Innovators (A4I) – a programme run by Innovate UK, the UK’s innovation agency – we recently undertook a “deep dive” into the nature and extent of parasitic (off-axis) motion errors in Queensgate’s multi-axis nanopositioning stages. Working with NPL scientists, this granular investigation yielded a practical correction and calibration methodology to reinforce end-to-end quality assurance across the Queensgate portfolio of piezo-driven nanopositioning stages (as well as enabling technologies such as piezo actuators, capacitive sensors, control electronics and software).
What does the development roadmap look like for your portfolio of positioning products in 2024?
Near term, we will be launching our new high-load positioners – for manoeuvring the full optical head in a non-contact surface metrology system – as well as adding multi-axis capability to our range of sample positioning stages for 300 mm wafers (with load capacity to support heavy wafer chucks). Also in prototype development, and due for full commercial release later this year, is a Z-axis tip/tilt sample stage for advanced silicon-wafer processing. The key take-away: working together, Prior Scientific and Queensgate can cover all your positioning requirements for 3D surface measurement and inspection.
Enabling technologies and subsystems for 3D surface measurement
From research microscopes to automated surface imaging systems, Prior Scientific provides motorized positioning stages, robotic loaders, illumination solutions and other core subsystems to support the metrology requirements of advanced semiconductor R&D and manufacturing.
Prior’s H105F, for example, is a motorized XY stepper-motor stage (154 x 154 mm travel) that can accommodate large samples including semiconductor wafers, photomasks and printed circuit boards. Part of the same product family, the H112 provides a maximum travel range of 302 x 302 mm to accommodate 300 mm wafers (while ensuring compatibility with many robot-arm wafer loaders).
In parallel, Prior produces a range of motorized and manual objective nosepiece assemblies to integrate into new or existing custom optical systems. The nosepieces range from a single-objective fixed magnification for OEM applications to a six-position motorized nosepiece for automated scanning applications requiring multiple objectives.
Dovetailing with the Prior Scientific product offering, sister company Queensgate manufactures high-speed, high-precision piezo stages and capacitive sensors with low picometre resolutions for nanopositioning systems used in semiconductor wafer and mask inspection.
The WP-Z-120A wafer positioning system is a case in point. Designed for high-throughput applications, the stage combines millisecond response times with friction-free motion over a 120 µm closed-loop range. The product can handle 300 mm wafers and wafer chucks up to 8 kg.
Other core subsystems in the Queensgate portfolio include the OP400 and OP800 piezo objective scanners – offering up to 400 and 800 µm of travel respectively, with capacitive sensors giving sub-nm positioning resolution and repeatability. Meanwhile, OEM options are available now for a family of “high-load” Z positioners for positioning the entire optical system in a 3D surface metrology set-up (and compatible with loads up to 15 kg and travel ranges up to 300 µm).
- SEO Powered Content & PR Distribution. Get Amplified Today.
- PlatoData.Network Vertical Generative Ai. Empower Yourself. Access Here.
- PlatoAiStream. Web3 Intelligence. Knowledge Amplified. Access Here.
- PlatoESG. Carbon, CleanTech, Energy, Environment, Solar, Waste Management. Access Here.
- PlatoHealth. Biotech and Clinical Trials Intelligence. Access Here.
- Source: https://physicsworld.com/a/semiconductor-metrology-positioning-is-key/